पोरोसिटी, ठोसीकरणको क्रममा ग्यास इन्ट्र्यापमेन्टले गठन हुने गुहा-प्रकारको अवरोधहरू, MIG वेल्डिङमा सामान्य तर बोझिलो दोष हो र धेरै कारणहरू भएको एउटा हो। यो अर्ध-स्वचालित वा रोबोटिक एप्लिकेसनहरूमा देखा पर्न सक्छ र दुबै अवस्थामा हटाउने र पुन: कार्यको आवश्यकता पर्दछ - डाउनटाइम र बढ्दो लागतहरू।
स्टील वेल्डिङमा पोरोसिटीको प्रमुख कारण नाइट्रोजन (N2) हो, जुन वेल्डिङ पूलमा संलग्न हुन्छ। जब तरल पोखरी चिसो हुन्छ, N2 को घुलनशीलता उल्लेखनीय रूपमा कम हुन्छ र N2 पग्लिएको स्टीलबाट बाहिर निस्कन्छ, बुलबुले (छिद्रहरू) बनाउँछ। ग्याल्भेनाइज्ड/गल्भेनियल वेल्डिङमा, बाष्पीकरण गरिएको जिंकलाई वेल्डिङ पूलमा हाल्न सकिन्छ, र यदि पोखरी बलियो हुनु अघि भाग्न पर्याप्त समय छैन भने, यसले पोरोसिटी बनाउँछ। एल्युमिनियम वेल्डिङको लागि, सबै पोरोसिटी हाइड्रोजन (H2) को कारणले हुन्छ, जसरी N2 स्टीलमा काम गर्दछ।
वेल्डिंग पोरोसिटी बाह्य वा आन्तरिक रूपमा देखा पर्न सक्छ (प्रायः उप-सतह पोरोसिटी भनिन्छ)। यो वेल्डको एकल बिन्दुमा वा सम्पूर्ण लम्बाइमा पनि विकास गर्न सक्छ, कमजोर वेल्डहरूको परिणाम स्वरूप।
पोरोसिटीका केही मुख्य कारणहरू कसरी पहिचान गर्ने र तिनीहरूलाई कसरी द्रुत रूपमा समाधान गर्ने भनेर जान्दा गुणस्तर, उत्पादकता र तल्लो रेखा सुधार गर्न मद्दत गर्न सक्छ।
खराब शिल्डिंग ग्यास कवरेज
कमजोर सुरक्षा ग्यास कभरेज वेल्डिंग पोरोसिटीको सबैभन्दा सामान्य कारण हो, किनकि यसले वायुमण्डलीय ग्यासहरू (N2 र H2) वेल्ड पूललाई दूषित गर्न अनुमति दिन्छ। उचित कभरेजको अभाव धेरै कारणहरूका लागि हुन सक्छ, जसमा कमजोर सुरक्षा ग्यास प्रवाह दर, ग्यास च्यानलमा चुहावट, वा वेल्ड सेलमा धेरै हावा प्रवाह समावेश छ तर सीमित छैन। धेरै छिटो हुने यात्रा गति पनि एक अपराधी हुन सक्छ।
यदि एक अपरेटरले खराब प्रवाहको कारण समस्या उत्पन्न भएको शंका गर्छ भने, दर पर्याप्त छ भनेर सुनिश्चित गर्न ग्यास प्रवाह मिटर समायोजन गर्ने प्रयास गर्नुहोस्। स्प्रे ट्रान्सफर मोड प्रयोग गर्दा, उदाहरणका लागि, 35 देखि 50 घन फीट प्रति घण्टा (cfh) प्रवाह पर्याप्त हुनुपर्छ। उच्च amperages मा वेल्डिंग प्रवाह दर मा वृद्धि आवश्यक छ, तर यो धेरै उच्च दर सेट गर्न महत्त्वपूर्ण छ। यसले केही बन्दुक डिजाइनहरूमा अशान्ति निम्त्याउन सक्छ जसले ढाल ग्यास कभरेजमा बाधा पुर्याउँछ।
यो नोट गर्न महत्त्वपूर्ण छ कि फरक डिजाइन गरिएका बन्दुकहरूमा फरक ग्याँस प्रवाह विशेषताहरू छन् (तल दुई उदाहरणहरू हेर्नुहोस्)। शीर्ष डिजाइनको लागि ग्यास प्रवाह दरको "मीठो स्थान" तलको डिजाइनको भन्दा धेरै ठूलो छ। यो वेल्डिङ इन्जिनियरले वेल्ड सेल सेटअप गर्दा विचार गर्न आवश्यक छ।
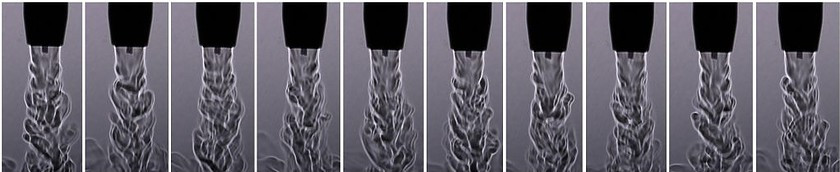
डिजाइन १ ले नोजल आउटलेटमा सहज ग्यास प्रवाह देखाउँछ
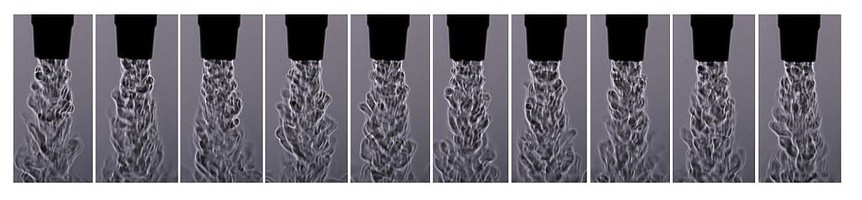
डिजाइन २ ले नोजल आउटलेटमा अशान्त ग्यास प्रवाह देखाउँछ।
साथै MIG वेल्डिङ बन्दुकको पावर पिनमा रहेको ग्यासको नली, फिटिङ र कनेक्टरहरू र ओ-रिङहरूमा क्षति भएको जाँच गर्नुहोस्। आवश्यक रूपमा बदल्नुहोस्।
वेल्ड सेलमा अपरेटरहरू वा भागहरू चिसो गर्न फ्यानहरू प्रयोग गर्दा, तिनीहरूले ग्यास कभरेजमा बाधा पुर्याउन सक्ने वेल्डिङ क्षेत्रमा सीधै औंल्याइएनन् भन्ने कुरामा ध्यान दिनुहोस्। बाहिरी हावाको प्रवाहबाट जोगाउन वेल्ड सेलमा स्क्रिन राख्नुहोस्।
चापको वांछित लम्बाइमा निर्भर गर्दै, सामान्यतया ½ देखि 3/4 इन्चको उपयुक्त टिप-टु-वर्क दूरी छ भनी सुनिश्चित गर्न रोबोटिक अनुप्रयोगहरूमा कार्यक्रमलाई पुन: छुनुहोस्।
अन्तमा, ढिलो यात्रा गति यदि पोरोसिटी रहिरहन्छ वा राम्रो ग्यास कभर्यागको साथ विभिन्न फ्रन्ट-एन्ड कम्पोनेन्टहरूको लागि MIG बन्दुक आपूर्तिकर्तासँग परामर्श गर्नुहोस्।
आधार धातु प्रदूषण
आधार धातुको प्रदूषण पोरोसिटी हुने अर्को कारण हो - तेल र ग्रीस देखि मिल स्केल र खिया सम्म। आर्द्रताले पनि विशेष गरी एल्युमिनियम वेल्डिङमा यो विच्छेदलाई प्रोत्साहित गर्न सक्छ। यी प्रकारका प्रदूषकहरूले सामान्यतया बाह्य पोरोसिटीमा नेतृत्व गर्छन् जुन अपरेटरलाई देखिन्छ। ग्याल्भेनाइज्ड स्टील सबसर्फेस पोरोसिटीको लागि बढी प्रवण हुन्छ।
बाहिरी पोरोसिटी विरुद्ध लड्न, वेल्डिंग गर्नु अघि आधार सामग्री राम्ररी सफा गर्न निश्चित हुनुहोस् र धातु-कोर्ड वेल्डिंग तार प्रयोग गर्ने विचार गर्नुहोस्। यस प्रकारको तारमा ठोस तार भन्दा उच्च स्तरको डिअक्सिडाइजरहरू छन्, त्यसैले यो आधार सामग्रीमा कुनै पनि बाँकी प्रदूषकहरूलाई बढी सहनशील हुन्छ। यी र अन्य कुनै पनि तारहरूलाई सधैं बिरुवा भन्दा समान वा अलि बढी तापक्रम भएको सुख्खा, सफा क्षेत्रमा भण्डार गर्नुहोस्। यसो गर्दा वेल्ड पूलमा ओसिलो परिचय गराउन र पोरोसिटी निम्त्याउन सक्ने सघनतालाई कम गर्न मद्दत गर्नेछ। चिसो गोदाम वा बाहिर तारहरू भण्डारण नगर्नुहोस्।
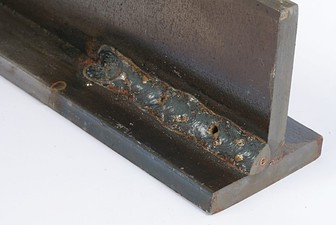
पोरोसिटी, ठोसीकरणको क्रममा ग्यास इन्ट्र्यापमेन्टले गठन हुने गुहा-प्रकारको अवरोधहरू, MIG वेल्डिङमा सामान्य तर बोझिलो दोष हो र धेरै कारणहरू भएको एउटा हो।
गैल्भेनाइज्ड स्टील वेल्डिङ गर्दा, जस्ता स्टील पग्लने भन्दा कम तापक्रममा वाष्पीकरण हुन्छ, र छिटो यात्रा गतिले वेल्ड पूललाई छिटो फ्रिज बनाउँछ। यसले स्टीलमा जस्ता वाष्पलाई जालमा पार्न सक्छ, जसको परिणामस्वरूप पोरोसिटी हुन्छ। यात्रा गति अनुगमन गरेर यो स्थिति लड्नुहोस्। फेरि, विशेष रूपमा डिजाइन गरिएको (फ्लक्स सूत्र) धातु-कोर गरिएको तारलाई विचार गर्नुहोस् जसले वेल्डिंग पूलबाट जिंक भाप बचाउनलाई बढावा दिन्छ।
भरिएको र/वा कम आकारको नोजलहरू
भरिएको र/वा सानो आकारको नोजलले पनि पोरोसिटी निम्त्याउन सक्छ। वेल्डिङ स्प्याटर नोजलमा र कन्ट्याक्ट टिप र डिफ्युजरको सतहमा निर्माण हुन सक्छ जसले गर्दा सिल्डिङ ग्यास प्रवाहमा प्रतिबन्ध लगाइन्छ वा यसलाई अशान्त बनाउँछ। दुबै अवस्थाहरूले अपर्याप्त सुरक्षाको साथ वेल्ड पूल छोड्छन्।
यस अवस्थालाई कम्पाउन्ड गर्नु एउटा नोजल हो जुन अनुप्रयोगको लागि धेरै सानो छ र ठूलो र छिटो स्प्याटर निर्माणको लागि बढी प्रवण छ। साना नोजलहरूले राम्रो संयुक्त पहुँच प्रदान गर्न सक्छन्, तर ग्यास प्रवाहको लागि अनुमति दिइएको सानो क्रस-सेक्शनल क्षेत्रको कारणले ग्यास प्रवाहलाई पनि अवरोध गर्दछ। नोजल स्टिकआउट (वा विश्राम) मा सम्पर्क टिपको चरलाई सधैं ध्यानमा राख्नुहोस्, किनकि यो अर्को कारक हुन सक्छ जसले तपाईंको नोजल चयनको साथमा ग्यास प्रवाह र पोरोसिटीलाई असर गर्छ।
त्यो दिमागमा, निश्चित गर्नुहोस् कि नोजल अनुप्रयोगको लागि पर्याप्त ठूलो छ। सामान्यतया, ठूला तार साइजहरू प्रयोग गरेर उच्च वेल्डिङ करेन्ट भएका अनुप्रयोगहरूलाई ठूला बोर साइजको नोजल चाहिन्छ।
अर्ध-स्वचालित वेल्डिङ अनुप्रयोगहरूमा, आवधिक रूपमा नोजलमा वेल्डिङ स्प्याटर जाँच गर्नुहोस् र वेल्डरको चिमटा (वेलपर) प्रयोग गरी हटाउनुहोस् वा आवश्यक भएमा नोजल बदल्नुहोस्। यो निरीक्षणको क्रममा, सम्पर्क टिप राम्रो आकारमा छ र ग्यास डिफ्यूजरमा स्पष्ट ग्यास पोर्टहरू छन् भनी पुष्टि गर्नुहोस्। अपरेटरहरूले एन्टि-स्प्याटर कम्पाउन्ड पनि प्रयोग गर्न सक्छन्, तर तिनीहरूले नोजललाई कम्पाउन्डमा धेरै टाढा वा धेरै लामो समयसम्म डुबाउन नदिने ख्याल राख्नुपर्छ, किनकि कम्पाउन्डको अत्यधिक मात्राले शिल्डिङ ग्यासलाई दूषित गर्न सक्छ र नोजल इन्सुलेशनलाई क्षति पुर्याउन सक्छ।
रोबोटिक वेल्डिङ सञ्चालनमा, स्प्याटर बिल्डअपको सामना गर्न नोजल क्लिनिङ स्टेशन वा रिमरमा लगानी गर्नुहोस्। यो परिधीयले उत्पादनमा नियमित पजको समयमा नोजल र डिफ्यूजर सफा गर्छ ताकि यसले चक्र समयलाई असर गर्दैन। नोजल क्लिनिङ स्टेसनहरू एन्टी-स्प्याटर स्प्रेयरसँग संयोजनमा काम गर्ने उद्देश्यले गरिन्छ, जसले कम्पाउन्डको पातलो कोट अगाडिको भागहरूमा लागू गर्दछ। धेरै वा धेरै थोरै एन्टि-स्प्याटर फ्लुइडले अतिरिक्त पोरोसिटीको परिणाम हुन सक्छ। नोजल सफा गर्ने प्रक्रियामा एयर ब्लास्ट थप्दा पनि उपभोग्य वस्तुहरूबाट खुकुलो स्प्याटर हटाउन मद्दत गर्न सक्छ।
गुणस्तर र उत्पादकता कायम राख्न
वेल्डिङ प्रक्रियाको अनुगमन गर्न ध्यान दिएर र पोरोसिटीको कारणहरू थाहा पाउँदा, समाधानहरू कार्यान्वयन गर्न अपेक्षाकृत सरल छ। त्यसो गर्नाले अझ बढी चाप-अन-समय, गुणस्तरीय नतिजाहरू र उत्पादनको माध्यमबाट चल्ने थप राम्रो भागहरू सुनिश्चित गर्न मद्दत गर्न सक्छ।
पोस्ट समय: फेब्रुअरी-02-2020